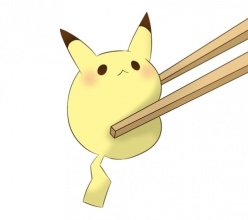
常压炉是炼油厂常减压蒸馏装置的重要设备之一,也是装置主要的耗能设备,其能耗占常减压蒸馏装置总能耗的50%以上。常减压蒸馏装置常压炉设计负荷为27.9MW,目前实际运行负荷为34.9MW,在目前满负荷运行工况下.从常压炉对流室出来的烟气排烟温度为350℃左右,流量为67dma3/h,携带热量为6.98MW,该热管散热器热量占常压炉负荷的20%,占装置总能耗的15%。这部分热管散热器热量价值可观,能否有效回收对常减压蒸馏装置达标和节能降耗工作至关重要。
◆改造前余热回收系统预热热管散热器存在问题
原设计余热回收系统采用的是回转式空气预热热管散热器,该预热热管散热器存在以下问题:
一、漏风量大。由于回转式预热热管散热器的转动面和固定面存在空隙,再加上空气侧和烟气侧存在较大压差,这样易使空气在转子处发生“短路”,且由于长周期的运行产生的变形磨损和腐蚀,往往造成实际漏风系数远远大于设计漏风系数.最大漏风量可达30%左右,这样也就造成了不必要的能量浪费。
二、故障率较高。由于回转式预热热管散热器转动部件校多,如转子、齿轮油泵、减速器、齿轮箱等,为维持这些转动部件正常运行,还需要配备复杂的润滑管路系统。实际运行过程中,由于蓄热片积灰造成转子失去动平衡或蓄热片脱落卡住造成驱动电机跳闸,润滑管路泄漏,转子轴承失效等故障经常发生,如1997年全年预热热管散热器各类故障达12次,非正常停运时间52d,严重影响了装置的安全平稳生产,成为威胁装置安全生产的一大隐患。
三、压力降大。多层波纹形状的蓄势片相互叠加构成了回转式预热热管散热器的传热主体,蓄热片的波纹形状显然增加了传热面积和传热系数,但也同时增加了预热器的压力降,且由于燃料油中含有大量的金属盐类杂质(如Fe,Ni,Na,Ca,Mg,V等)和浮尘,燃烧后吸附在高温烟气中大量的碳粒子上,到达空气预热器时,流速降低,温度降低,就凝结、吸附在蓄热片上,逐渐积累,产生灰垢。由于蓄热片的波纹形状加之积灰粘性极强,一般的吹灰方法很难将灰垢较好的除去,因而产生流道堵塞,增加了预热热管散热器的压力降,降低了热导率。同时这些灰垢附着在蓄热片上,易产生垢下腐蚀,造成蓄热片脱落,影响预热热管散热器安全运行。